Bridgestone tirematics realise “tire-as-a-service” business model to improve customer value with 0G Network
Tire pressure monitoring systems (TPMS) have been widely deployed to address safety and environmental issues on all types of vehicles across the globe. Currently, the European Union, the United States, South Korea, and China have introduced TPMS legislation. Japan, India, Russia, Malaysia, the Philippines, and Indonesia also moving towards legislation for the implementation of TPMS regulations.
The goal of a TPMS is avoiding traffic accidents, poor fuel economy, and increased tire wear thanks to under-inflated tires through early recognition of a hazardous state of the tires.
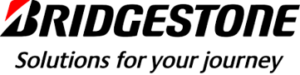
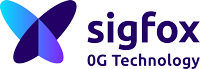
Bridgestone Tire Solution Japan is a group company of Bridgestone Corporation, a Japanese multinational tire manufacturer founded in 1931.
Challenges
18% of trucks have poorly maintained tires, and 37% of these are underinflated. When performed manually, tire pressure measurement is slow, unreliable, and disrupts supply chains and business operations if vehicles need unplanned maintenance.
Solution
Tirematics is a tire pressure monitoring solution by Bridgestone Tire Solutions Japan that shares tire pressure information with transportation companies in Japan, such as truck and bus operators, through the cloud. A compact sensor in the tire connects to the Sigfox 0G network operated by KYOCERA Communications Systems (KCCS) in Japan. The 0G Network is a global, public, low-power, long-range network enabling massive IoT, designed for low-cost, energy-efficient device connectivity.
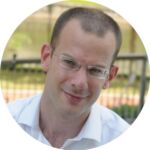
Tirematics is core to Bridgestone’s commitment to continuously improve customer and social value with sustainable solutions. The simple fit-and-forget solution combined with 0G Network connectivity ensures Tirematics reduces safety and business challenges caused by tire pressure abnormalities and helps Bridgestone realise its “tire as a service” business model to better manage tires through the entire lifecycle.
Thierry Jakircevic, Digital Solution Platform Planning and Development Div. Director at Bridgestone Corporation
Benefits
Customer benefits Tirematics delivers with remote monitoring, accurate data into tire pressure include:
- Accident prevention and reduced vehicle breakdowns.
- Better mileage and fuel economy.
- Decreased operational and maintenance costs.
- Improved customer service and satisfaction through fewer operational disruptions.
- Positive social impact, such as better resource productivity, recycling, and fewer CO2 emissions.
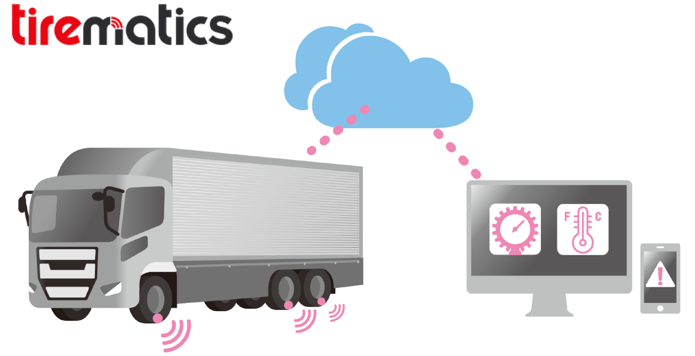
Before the introduction of TPMS, tire pressures were manually taken by pressure gauges, but after the introduction of TPMS, monitoring tire pressure became much more efficient since sensor readings will be taken remotely and in real time, improving the productivity of the operational team.Naoki Kawai, Deputy Division Manager, Wireless Solutions Division at KYOCERA Communication Systems Co., Ltd
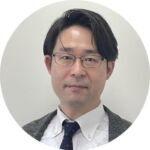